1.1 Introduction to the working principle of injection molding
The working principle of injection molding machine is similar to that of syringe infusion. It uses the thrust of screw (or plunger) to inject the plastic that has been plasticized into the closed injection mold cavity at high pressure and high speed. After cooling and curing, plastic products with the shape of the mold cavity are obtained. Injection molding is a cyclic process, each cycle mainly includes: quantitative feeding a melting plasticizing a pressure injection a filling cooling a mold lifting parts. After removing the plastic part, the mold is closed again and the next cycle is carried out.
1.2 Application of injection molding machine
Injection molding processing method can be shaped complex shape, complex structure, high dimensional precision and plastic products with inlays. It has strong adaptability to the processing of various plastic materials, so it is widely used in household appliances, automobiles, aviation, instruments, national defense, telecommunications, medical treatment, construction and daily necessities and other industries, and has a wide range of uses.
1.3 Classification of injection molding machine
Injection molding machine is divided into plunger type, screw plunger type and reciprocating screw type injection molding machine according to plasticizing way, especially the past compound screw type is the most common; According to the transmission mode of the closing device can be divided into hydraulic, mechanical and hydraulic mechanical (connecting rod) type; According to the axis of the injection device and the axis of motion of the closing device, it can be divided into horizontal injection molding machine, vertical injection molding machine, Angle injection molding machine and multi-station injection molding machine, among which the horizontal injection molding machine is the most common.
(1) Classification of plasticizing methods
① Plunger injection molding machine
The characteristic is that the plasticizing parts are the barrel and the plunger. The plastic entering the barrel is heated by the barrel, and the injection molding process is promoted by the plunger. However, due to the lack of mixing of the melt in the cylinder, the temperature difference between the melt is great, and the temperature distribution of the melt is not uniform.
Figure 1. Structure diagram of plug injection molding machine
② Screw plunger injection molding machine
The plasticizing device of this injection molding machine is separated from the injection device. The parts that plasticize the rubber are the screw and the barrel, and the injection part is completed by the plunger. The rubber material is first uniformly plasticized in the plasticizer barrel by the screw, then enters the injection barrel by the check valve, and finally is pushed into the mold cavity by the plunger.
FIG. 2 Structure diagram of screw plug injection molding machine
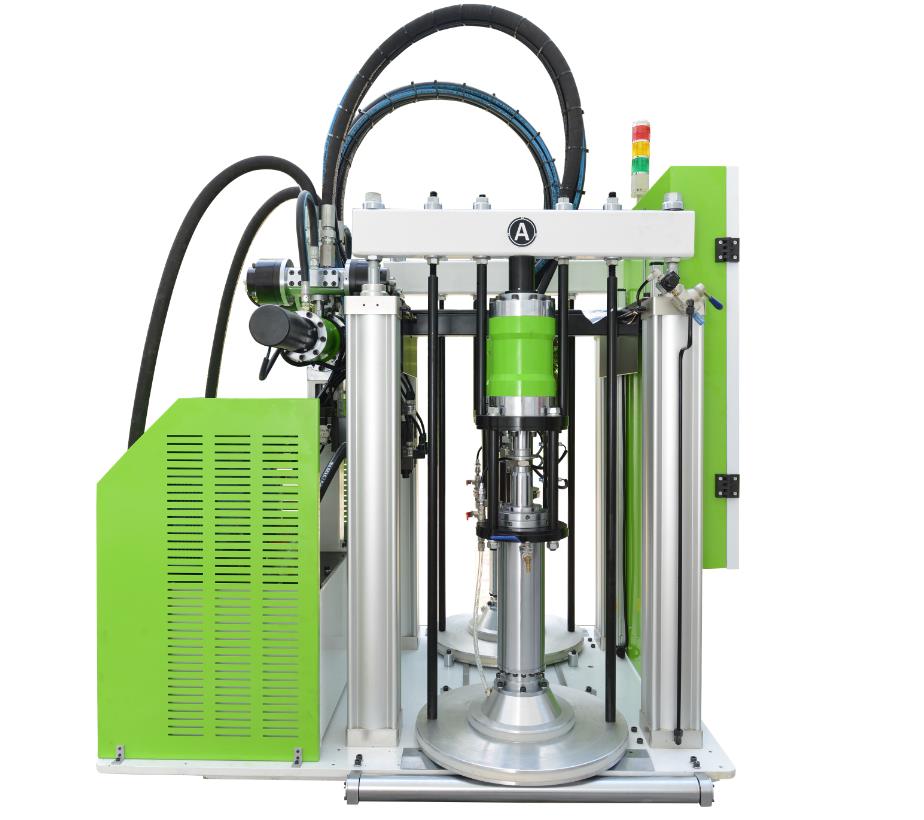
plastic injection molding machine
Reciprocating screw injection molding machine
The plastic parts of the injection molding machine are the screw and the barrel. The rubber material entering the barrel is not only heated by the barrel, but also softened by the shear heat and friction heat generated by the rotation of the screw. The injection process is completed by a screw. In the plasticization process, due to the rotation of the screw, the plastic melt not only has axial movement, but also has lateral flow and cyclotron movement. These different forms of movement greatly promote the mixing effect of the plastic melt, so that the temperature in the melt reaches a high degree of uniformity. And the screw is one side of the rotation of plasticizing and backward measurement, its plasticizing capacity is large, plasticizing quality is good. So reciprocating screw injection molding machine is widely used.
FIG. 3 Structure diagram of reciprocating screw injection molding machine
(2) Classification by mold closing device
① All mechanical
Mechanical mold closing device refers to the mechanism action to the generation and maintenance of mold locking force are completed by mechanical transmission, also known as the full mechanical mold closing device. Early injection molding machines are all mechanical mold closing device injection molding machines, but because the adjustment of mold closing force and mold speed is more complex, inertia impact and noise, maintenance is difficult, there are few manufacturers.
② Full hydraulic type
Hydraulic clamping device refers to the production and maintenance of clamping action to clamping force are realized by hydraulic transmission system. Hydraulic mode closing device is safe, reliable, low noise, and can easily adjust the speed and force of mold closing. But there are hydraulic oil leakage and pressure fluctuation and the rigidity of the system is weak.
③ Hydraulic – mechanical type
Hydraulic-mechanical die closing device is composed of hydraulic system and mechanical elbow system, and has the advantages and disadvantages of both mechanical and hydraulic die closing devices. Currently it is the most commonly used model of thermoplastic injection molding machine.
④ Electric-mechanical type
The electric-mechanical mold closing device is composed of servo motor, winding gear belt, screw, bending elbow mechanism and so on. This type of closing device has no hydraulic pressure, can avoid oil leakage problems, and has the advantages of energy saving, low noise, clean, easy to operate and maintain. At present, most dust-free workshops use this kind of mold closing device.
(3) Classification by way of arrangement
① Horizontal injection molding machine
This is the most common type. The mold closing part and the injection part are on the same horizontal center line, and the mold is opened along the horizontal direction. Its characteristics are: the fuselage is low, easy to operate and maintain; Low center of gravity, stable installation; After ejecting products can use gravity to automatically fall, easy to realize automatic operation. At present, the injection molding machine on the market mostly uses this type.
② Vertical injection molding machine:
The mold closing part and the injection part are on the same vertical center line, and the mold is opened in a vertical direction. Therefore, its footprint is small, easy to place inserts, loading and unloading mold is more convenient, the material falling into the hopper can be plasticized more evenly. But the product is not easy to fall automatically after ejecting, must be taken off by hand, not easy to achieve automatic operation. Vertical injection molding machine is suitable for small injection molding machine, generally in 60 grams below the injection molding machine is used more, large and medium-sized machine should not be used.
Figure 4 Horizontal and vertical injection molding machine outline
③ Angle injection molding machine:
Its injection direction and die interface in the same surface, it is especially suitable for machining center parts do not allow gate traces of flat products. It covers an area smaller than the horizontal injection molding machine, but the insert into the mold is easy to tilt down. This type of injection molding machine is suitable for small machines.
Figure 5. Shape diagram of Angle injection molding machine
④ Multi-mold rotary disk injection molding machine:
It is a special injection molding machine with multi-station operation. Its characteristic is that the mold closing device adopts the rotating disk structure and the mold rotates around the rotating shaft. This type of injection molding machine gives full play to the plasticizing ability of the injection device, can shorten the production cycle, improve the production capacity of the machine, so it is especially suitable for the cooling setting time is long or because of the placement of inserts and need more auxiliary time for the production of mass products. But because of the large and complex system, the closing force of the closing device is often small, so this injection molding machine is widely used in the production of plastic soles and other products.
1.4 Structure and parameters of injection molding machine
Injection molding machine includes injection device, closing device, transmission system and electrical control system.
Figure 6. Outline of injection molding machine
Figure 7 Structure diagram of injection molding machine
The basic requirements of injection molding are plasticizing, injection and shaping. Plasticization is the premise to realize and guarantee the quality of the molding products, and in order to meet the requirements of molding, injection must ensure that there is enough pressure and speed. At the same time, due to the high injection pressure, the corresponding high pressure in the mold cavity (the average pressure in the mold cavity is generally between 20 and 45MPa), so there must be a large enough mold closing force. It can be seen that the injection device and the mold device are the key parts of the injection molding machine.
1.4.1 Injection system structure and parameters
1.4.1.1 Injection system structure and composition
The main components of the injection system include plasticizing injection device, screw drive device and measuring device. The following figure shows the main components of the screw reciprocating injection molding machine.
Figure 7 Main components of the injection system
(1) Plasticizing injection device
Mainly including screw, barrel (barrel) and heating element, in the head of the screw can also be arranged to prevent the reverse flow of melt or a variety of shear mixing head.
① Screw:
The injection screw has the function of plasticizing the plastic material and injecting the melt into the mold cavity. During plasticizing, the heating of the barrel and the rotation of the screw make the rubber material change from solid to viscous flow melt in the process of forward transportation; During injection, the screw moves forward to inject the melt at the front of the barrel into the mold cavity. The structure and working characteristics of screw have great influence on the production efficiency of injection molding machine and the quality of injection molding products.
The working characteristics of the screw: the screw moves axially in the plasticization and injection process; The work of the screw is interstitial, the plasticization process of the screw is unstable melting process, and the plasticization process is only the process of preparing the molten material for injection; After screw conveying and plasticizing, the rubber material still stays in the front section of the barrel for a period of time, and can still continue to accept the heating of the barrel and further plasticize.
Screw structure: In order to adapt to different properties of plastic processing requirements, the screw design for different structural forms. At present, the application of screw structure forms are: gradient type, mutation type and universal type.
Screw material: It is divided into full hard screw (SKD61, SKH-91 or HPT full hardening powder alloy steel), stainless steel screw (9Cr18Mov), double alloy screw (38CrMALA or SACM645 as the substrate), nitride screw (38CrMALA as the substrate), tungsten carbide screw (surface covered with cobalt and tungsten carbide composite alloy powder coating), plating Chrome screw, etc. The ordinary screw in our supplier is usually stainless steel screw or nitride screw; For fiber or V0 grade above the material, will generally use double alloy screw or tungsten carbide screw.
Screw classification is as follows:
Figure 7 Screw structure form
The graded screw is a screw with a long compression section (i.e., a melting section), characterized by a relatively gentle energy conversion during plasticization. As shown in FIG. 7 (a), the compression section L2 is long, and the depth of the screw groove in this section gradually becomes shallow from deep, and the energy conversion during plasticizing is relatively moderate. It is suitable for processing plastics with a wide melt temperature range, as such plastics require sufficient plasticizing process to melt completely. Gradient type screw is suitable for processing such as PS, PVC and other non-crystalline plastics with wide softening temperature range and high viscosity.
Mutant screw is a kind of screw with small compression section, which is characterized by intense energy conversion during plasticizing. As shown in FIG. 7 (b), the compression section L2 is short, and the depth of the screw groove in this section changes sharply from deep to shallow, and the energy conversion during plasticizing is relatively intense. Suitable for processing plastics with a narrow melt temperature range, because such plastics can be softened and melted in a short time as long as they have been preheated enough to reach the melting point. Mutant screw is suitable for processing polyamide and polyolefin crystalline plastics.
The compression length of the universal screw is between the gradient screw and the mutant screw. In order to avoid the production of different types of plastic materials to replace the screw, usually choose universal screw, at this time as long as the appropriate adjustment of the process parameters (such as cylinder temperature, screw speed and back pressure, etc.), can also meet the molding requirements of different plastic materials. As shown in Figure 7 (C), the length of compression section L2 is generally 4 to 5 pitch lengths. At the same time, it is suitable for the processing of both crystalline and non-crystalline plastics, considering not only the non-crystalline materials can not withstand the excessive shear plasticization of the mutant screw in the compression section, but also the technological characteristics of the crystalline materials that need enough preheating to soften and melt.
In order to avoid degradation of glue due to local overheating, it is necessary to cool and control the temperature of screw in production. At the beginning of injection molding machine manufacturing, most of the screw center hole into the flow of mineral oil for cooling; The heat pipe is now commonly used to cool the screw, which is characterized by the placement of a capillary suction core permeating the working liquid in the inner wall of the screw or the opening of a special oil tank. When the heat pipe works, the evaporation section of the heat pipe located in the metering section of the screw is heated, and the medium enclosed in it sublimates into steam and constantly flows back from the evaporation section to the condenser section of the heat pipe located in the plasticizing section of the screw is cooled to liquid. The liquid then flows to the evaporation section through the action of the capillary, forming a circulation. The medium in the heat pipe is water, oil and some organic solvents.
② Screw head
In the screw injection, for the rubber material with low viscosity, it is necessary to prevent the problems of low injection efficiency, large pressure loss and difficult pressure preservation caused by melt reflux. For the viscose material with higher viscosity, it is necessary to solve the problem of decomposition of hysteresis caused by incomplete discharge when injected, so the structure of the screw head has the form of check type screw head, prevent hysteresis decomposition type screw head and special purpose screw head.
FIG. 8 Reverse screw head
(3) Cylinder: the cylinder is generally a whole structure, there is a certain gap between the inner hole of the cylinder and the screw, and the external heating and cooling device is installed. Generally, 38CrMOALA surface nitriding is used, and tungsten carbide or HPT all-hardened powder alloy steel is used for fireproof V0 grade or fiber reinforced engineering plastics.