First, the working principle of injection molding machine
Injection molding machine for short injection molding machine.
Injection molding is the use of plastic thermophysical properties, the material from the hopper into the barrel, the barrel outside the heating ring heating, so that the material melt, in the barrel is equipped with external power motor drive rotating screw, material under the action of the screw, along the screw groove forward transportation and compaction, the material in the external heat and screw shear under the double action gradually plasticized, melting and homogenization, When the screw rotation, the material in the screw groove friction and shear force under the action, the molten material pushed to the head of the screw, at the same time, the screw in the material reaction backward, so that the head of the screw to form a storage space, complete the plasticization process, then, the screw in the injection cylinder piston thrust under the action, with high speed, high pressure, The molten material in the storage room is injected into the cavity of the mold through the nozzle. After the molten material in the cavity is kept under pressure, cooled and solidified, the mold is opened under the action of the mold closing mechanism, and the finished product is ejected from the mold through the ejecting device.
Two, the classification of injection molding machine
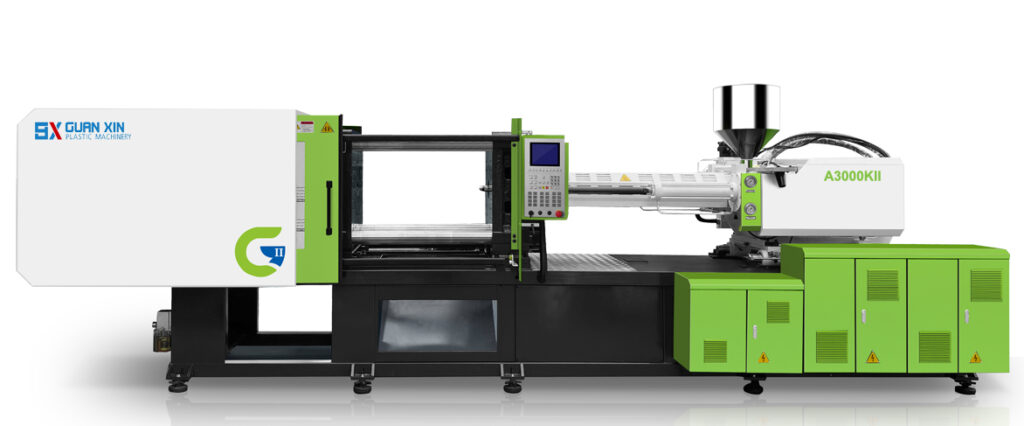
KII Series machine
There are three types of configuration according to the mold closing parts and injection parts: horizontal, vertical and Angle
(1) Horizontal injection molding machine: Horizontal injection molding machine is a very common type. It is characterized that the center line of the injection assembly is concentric or consistent with the center line of the closing assembly and parallel to the mounting ground. Its advantages are low center of gravity, stable work, mold installation, operation and maintenance are more convenient, mold open file, occupy space height is small; But covers a large area, large, medium and small machines are widely used.
(2) Vertical injection molding machine: its characteristic is that the axis of the closing device and the injection device is arranged in a line and perpendicular to the ground. It has the advantages of small floor area, convenient mold assembly and disassembly, easy installation of inserts, plasticizing of materials falling into the hopper more evenly, easy to realize automation and automatic line management of multiple machines. The disadvantage is that the ejecting product is not easy to fall off automatically, often need manual or other methods to take out, not easy to achieve full automatic operation and large product injection; High fuselage, feeding, maintenance inconvenience.
(3) Angle injection molding machine: the axes of the injection device and the mold device are arranged vertically. According to the relative position of the injection assembly center line and the installation base surface, there are horizontal, vertical and horizontal: (1) horizontal, injection assembly line and the base surface parallel, and the mold assembly center line and the base surface perpendicular; (2) Vertical horizontal, injection assembly center line is perpendicular to the base surface, and the mold assembly center line is parallel to the base surface. The Angle injection machine has the advantages of both horizontal and vertical injection machines. It is especially suitable for the mold with asymmetric geometric shape products with side sprue.
Three, injection molding machine structure analysis
Injection molding machine according to the injection molding process requirements is a mechanical and electrical integration of strong machine, mainly by injection parts, closing parts, fuselage, hydraulic system, heating system, control system, feeding device and so on. As shown in Figure 2.
Wechat photo _20190302110026
(1) Typical structure of injection molded parts
1. At present, the common injection device has single cylinder form and double cylinder form, our injection molding machine is double cylinder form, and are directly driven by hydraulic motor screw injection molding. Because of different manufacturers, different models of the machine its composition is not exactly the same, the following is a specific analysis of the machine used by our factory.
The composition of injection molding device of vertical machine and horizontal machine are shown in Figure 3 and Figure 4 respectively.
The working principle is: When preplasticizing, the screw in the plasticized part is driven by the hydraulic motor to rotate the main shaft, one end of the main shaft is connected with the screw key, and the other end is connected with the hydraulic motor key. When the screw rotates, the material is plasticized and the plasticized molten material is pushed to the storage chamber at the front end of the barrel. At the same time, the screw is backed up under the reaction of the material, and the thrust seat is backed up by the thrust bearing. Pull the piston rod straight back through the nut, complete the measurement, injection, the injection cylinder rod cavity oil through the bearing to push the piston rod to complete the action, the piston rod cavity oil to push the piston rod and screw to complete the injection action
Vertical injection molding machine has six systems: injection system, clamping system, hydraulic/hydraulic transmission system, electrical control system, heating/cooling system, lubrication system.
1: The jet system is one of the main features. There are three main forms: plunger type, screw type, and screw premolded plunger injection type. At present, screw type is the most widely used. Its role is in the cycle process of injection molding machine, in the specified time for a certain amount of plastic heating plasticizing, and then the molten plastic at a certain pressure and speed through the screw completely injected into the cavity.
2: clamping system is mainly composed of clamping device, adjusting mechanism, ejector mechanism, front and rear fixed template, moving template, clamping cylinder, safety protection mechanism seven parts. The closing system ensures that the mold is closed, opened and ejected. After the mold is closed, sufficient clamping force is provided to the mold to resist the pressure of the mold cavity caused by the molten plastic entering the mold cavity, so as to prevent the mold cracking and resulting in product defects.
3: Hydraulic system/hydraulic transmission system is mainly composed of various hydraulic components and hydraulic auxiliary components. Its power source is oil pump and motor. Control all kinds of hydraulic pressure and flow, can meet the requirements of various injection process. Its function is to provide power for various actions required by the injection molding machine process, to meet the pressure, speed and temperature of each part of the vertical injection molding machine and a series of requirements.
4: Electric control system of vertical injection molding machine by electronic control system and hydraulic system reasonable coordination, can realize the injection molding machine process requirements with pressure, temperature, speed, time and various procedures operation. It is mainly composed of electrical appliances, electronic components, meters, heaters, sensors and so on. Manual, semi-automatic, fully automatic and adjustment are four commonly used fuel injection control methods.
5: Heating/cooling system The heating system is mainly used to heat the cylinder and the nozzle. Generally, the electric heating coil is used as the heating device, which is installed outside the cylinder body, and the situation of the injection molding machine is detected by the thermocouple. The heat source of the material plasticized is formed through the heat conduction of the cylinder wall. The cooling system is mainly used to cool the oil temperature, which will cause a variety of failures, so the oil temperature must be controlled in time. The cooling position is close to the outlet of the feed pipe to prevent the raw material from melting at the outlet of the feed pipe, leading to the abnormal discharge and blockage of the raw material
6: The role of the lubrication system is to provide lubrication conditions for the motion template, adjusting device, connecting rod hinge and other relative moving parts of the vertical injection molding machine. Convenient to reduce energy consumption, improve parts life. Lubrication may be periodic manual lubrication or automatic electric lubrication.