First, classification of injection molding machine:
Due to the structure and variety of injection products, so used for molding injection products injection machine types are more.
1. Classify raw materials according to plasticizing and injection methods.
2. Classification according to the shape and structure of the injection machine.
3. Classification according to the processing capacity of injection molding machine.
4. Classification by special purpose of injection machine.
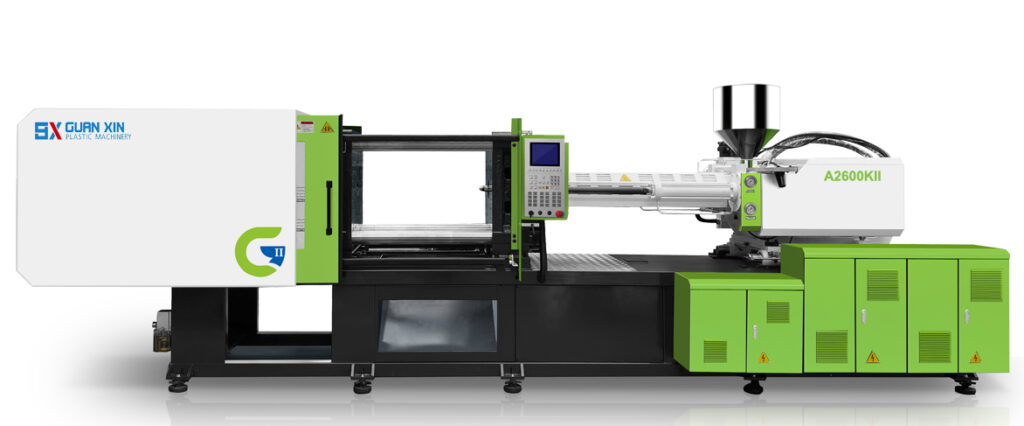
plastic injection molding machine
According to the classification of plasticizing and injection of raw materials, the injection molding machine can be divided into three kinds: (1) plunger type, (2) reciprocating screw type and (3) screw plasticizing plunger injection type.
According to the different shape and structure of the injection machine, it can be divided into (1) vertical injection molding machine, (2) horizontal injection machine, (3) Angle injection machine, (4) multi-mold injection machine, (5) combined injection machine
According to the size of the processing capacity of the injection machine classification, can be divided into (1) ultra-small injection machine, (2) small injection molding machine, (3) medium injection molding machine, (4) large injection machine (5) ultra-large injection molding machine
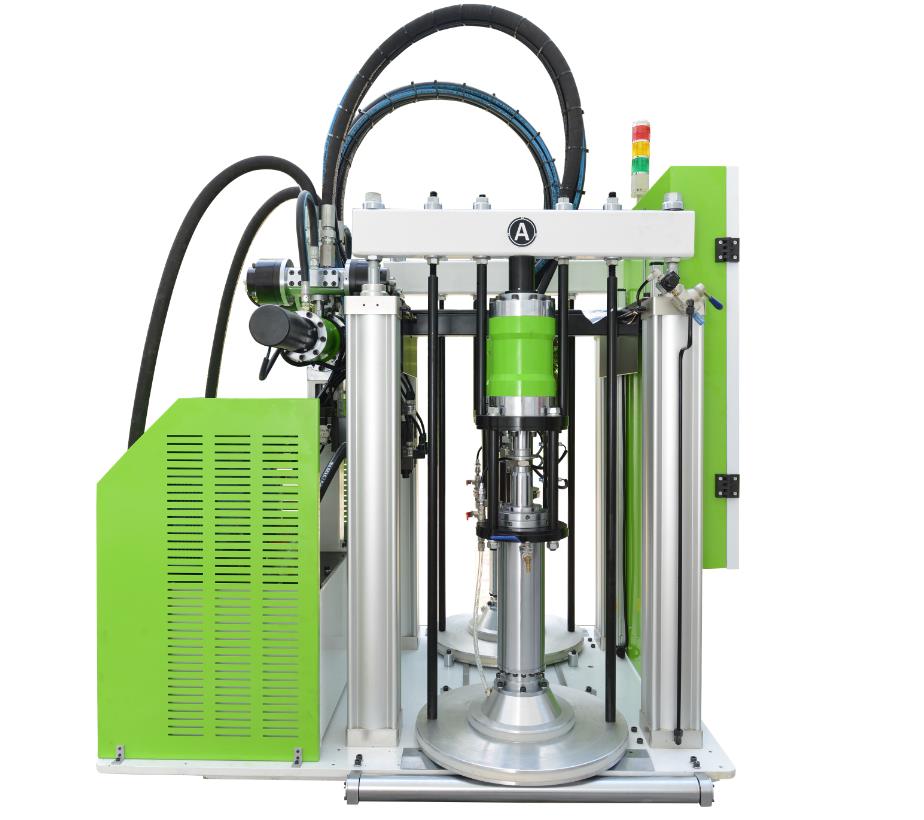
• Plastic Products Mould Making Machine
According to the purpose of the injection machine can be divided into (1) general injection machine, (2) exhaust injection machine, (3) precision high-speed injection machine, (4) plastic shoe injection machine, (5) three injection head single-mode injection machine, (6) double injection head two-mode injection machine
2. Comprehensive performance parameters of injection molding machine
The design and manufacture of injection molding machine is a more reasonable economic index, is to assess some of its comprehensive performance parameters, is to meet the production of qualified injection molding mouth outside the parameters, that is, the number of injection time and space cycles, total power of electricity, total quality of equipment and equipment dimensions.
The empty cycle time is composed of the switching time other than the mold closing time, the injection seat moving back and forth, the mold opening time, the plasticizing time, the injection time, the pressure retaining time, the cooling time and the taking out of the workpiece. It is also the idle time in the completion of a cycle of the product.
Empty cycle time is also an index to measure the production capacity of the injection machine, which reflects the quality of the mechanical structure, the sensitivity of the operation, the hydraulic system and the working quality of the electrical performance parameters.
In order to meet people’s large demand for injection products, to meet the market supply, DKM plastic industry engineers and technicians through continuous efforts, gradually to the injection product production of high-speed, automatic direction. The following measures are very good to improve the injection molding machine, quality sublimation.
1. Increase the number of cycles of injection molding machine per unit time: by improving the screw speed for plasticizing materials, accelerate the injection speed of molten material, in order to shorten the production cycle of single product injection molding, so as to achieve the effect of increasing the number of cycles.
2. One injection machine is equipped with two injection cylinders. The preplastic screw can feed the two injection cylinders successively to achieve continuous injection.
3. Use two sets of mold injection molding. When working, the two sets of molds rotate and transpose, so that the melting injection, cooling and mold opening processes are carried out at two stations at the same time, which shortens the waiting time of pre-plastic stop and nearly doubles the production capacity of the injection machine.
4. Realize automation: in the production process of injection molding products, the computer is used to control the delivery of raw materials, cylinder feeding, process temperature control, mold opening, parts taking out and other processes to implement automatic program control.
5. In order to make injection molding products can work in a variety of special environments, it is required to use different properties of plastics to produce plastic products that can adapt to a variety of working environments. Different properties of plastic products, its injection production process conditions are different, which promotes the injection machine to special development. Such as with good electrical properties, physical properties and heat resistance, not easy to deform products production with thermosetting plastic injection molding machine, a variety of colors, a variety of raw materials composite molding with multi-color injection machine, designed to improve product quality of the exhaust injection machine, fiber reinforced plastic injection machine, low foaming injection machine and injection blow molding machine.
6. In terms of injection molding production process, some have adopted flow injection molding, injection compression molding, sandwich injection molding, reaction injection molding and gas assisted injection molding, etc.
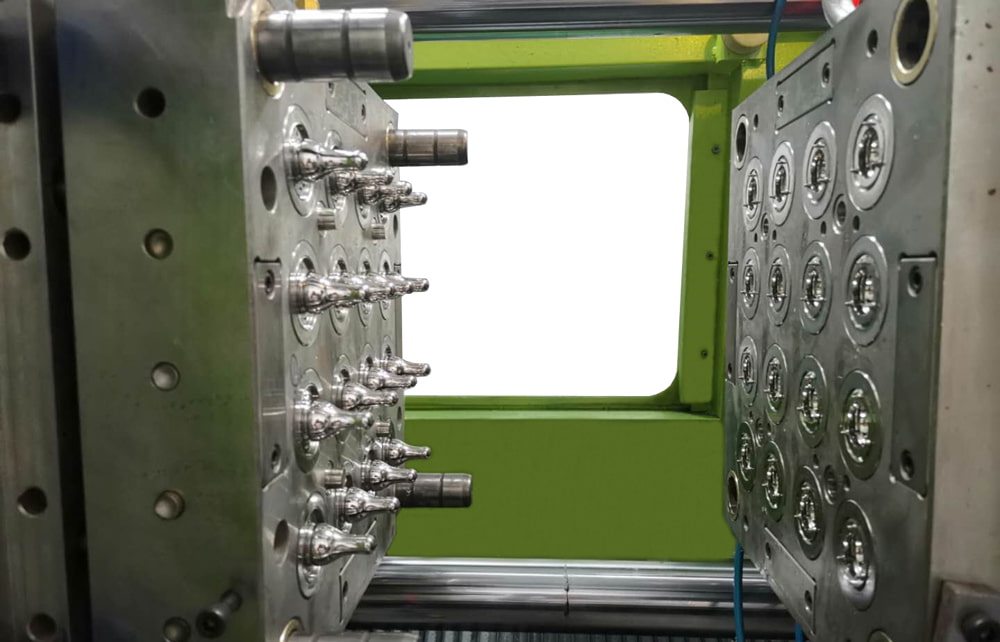
3 Advantages of high speed injection molding machine
1. Hydraulic system – High energy saving
2. Hydraulic system – rate
3. Electric control part – high precision
4. Mold closing system – high rigidity
5. Injection System – High response
6. Injection System – High plasticizing
7. High security
1. Stability, reliability, safety and service life of the machine. This is the most important factor to consider when purchasing injection molding machine. Because every consumer does not buy a product to solve a temporary need, but to use it for a long time. Therefore, the performance of the product itself is very important.
2. Technical parameters are also very important. No matter what kind of product we buy, we know its various performance through the relevant parameters. And consumers in the purchase of injection molding machine, the manufacturer can provide the relevant technical parameters of the same industry standards or domestic and foreign similar injection molding machine technical parameters compared, the larger gap belongs to defective products. In the process of comparison, careful comparison is needed to avoid omissions.
3. Machine maintenance and overhaul should be convenient. Maintenance can also be a factor when choosing a product. General products in the use of the process will appear some problems, then fast and convenient maintenance is very key.
4. The last but not the least point is the choice of suppliers. In general, consumers are willing to buy products from local manufacturers with service offices. Because the structure of injection molding machine is more complex, problems will inevitably occur in the process of use. At this time, the after-sales service of the product is very key, and this factor must be considered when choosing. And in general, injection molding machine manufacturers will directly choose direct sales, so that the price will be more affordable