Injection molding machine is a special equipment which combines the hot working characteristics of plastics with the principle of melting die casting of metals. The original plunger injection molding machine was not developed until the late 1940s until the preplasticized screw injection molding machine. Since then, the focus of development is mainly around the pre-plasticized screw injection molding machine, has since appeared twin screw, exhaust and other advanced forms.
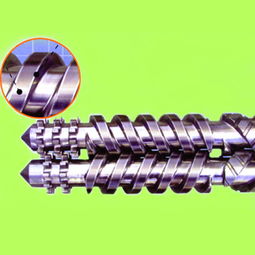
plastic injection molding machine
In 1980, France produced the world’s largest screw injection molding machine, with an injection capacity of 170kg. From the 1980s to recent years, the development of injection molding machine is mainly concentrated in several aspects: namely, the application of precision automatic control system and various auxiliary equipment in automatic molding; Precision machinery and high performance hydraulic system; Various special injection molding machine development and computer aided design of complex shape parts plastic flow analysis to determine the best injection conditions; Application of various energy saving technologies in injection molding machine.
Working principle of injection molding machine
Injection molding machine referred to as injection molding machine, injection molding is the use of plastic thermophysical properties, the material from the hopper into the barrel, the barrel outside by heating ring heating, so that the material melt, in the barrel is equipped with external power motor drive rotation of the screw, the material in the double action of the screw shear gradually plasticized, melting and homogenizing, when the screw rotation, Material in the groove friction force and shear force under the action of the molten material pushed to the head of the screw, at the same time, the screw in the material reaction backward, so that the head of the screw to form a storage space, complete the plasticization process, and then the screw in the injection cylinder piston reasoning under the action of high speed, high pressure, the storage room of the molten material through the nozzle into the mold cavity, After the molten material in the cavity is kept under pressure, cooled and solidified, the mold is opened under the action of the mold closing mechanism, and the finished product is ejected from the mold and dropped through the ejecting device.
Composition structure of injection molding machine
Injection molding machine according to the injection molding process requirements is a mechanical and electrical integration of a strong machine, mainly composed of injection parts, closing parts, frame, hydraulic system, heating system, control system, feeding device and so on.
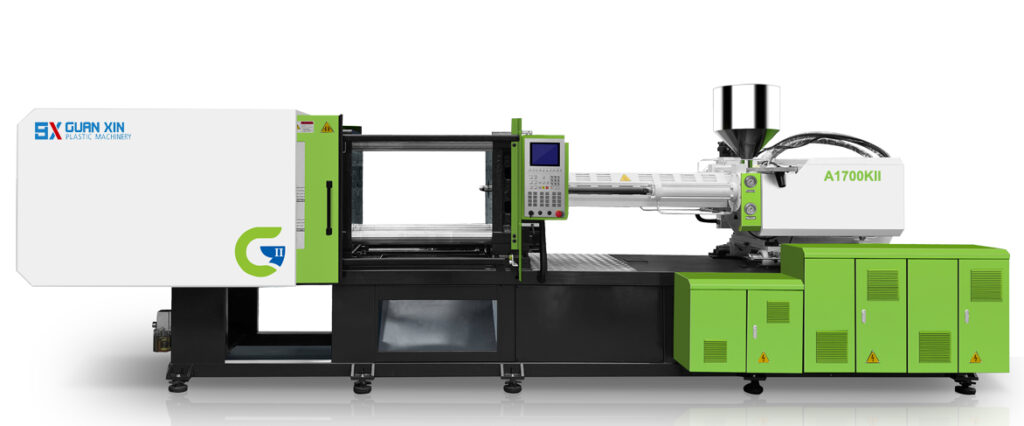
plastic injection molding machine
At present, the common injection molding device has single cylinder type and double cylinder type.
Plasticized parts have two kinds: plunger type and screw type. In the process of continuous rotation of the screw, the plastic realizes the change of physical state, and is finally injected into the mold cavity in a molten state. Therefore, the plasticized component is the core component to achieve uniform plasticizing and quantitative injection.
To provide customers with plastic products development, mold design, product manufacturing and injection molding, its products are widely used in every field of life today, such as household appliances, instruments, wires and cables, building equipment, communications electronics, automotive industry, aerospace, daily hardware and so on.
The overall production process of plastic products is: raw material selection – raw material coloring and matching – design casting mold – machine decomposition injection molding – printing – assembly detection of finished products – packaging factory.
Plastic products are made by injection molding or blow molding, so every time you design a sample, you have to open a new mold, and the mold is generally tens of thousands to hundreds of thousands of dollars, so in addition to the raw material price of plastic products, the cost of the mold is also very large. There may be many parts to make a finished product, and each part needs a separate mold. For example, the trash can is divided into: the barrel body — the lid, the liner, the handle several parts.
Generally speaking, the plastic factory refers to the processing of plastic products with plastic raw materials, semi-finished products and finished products, such as MP3 shell, telephone shell, mobile phone shell, computer monitor shell and other plastic accessories. And finished products such as plastic cups, plastic washbasins, plastic buckets, and other daily necessities. Its essence is called plastic processing plant.