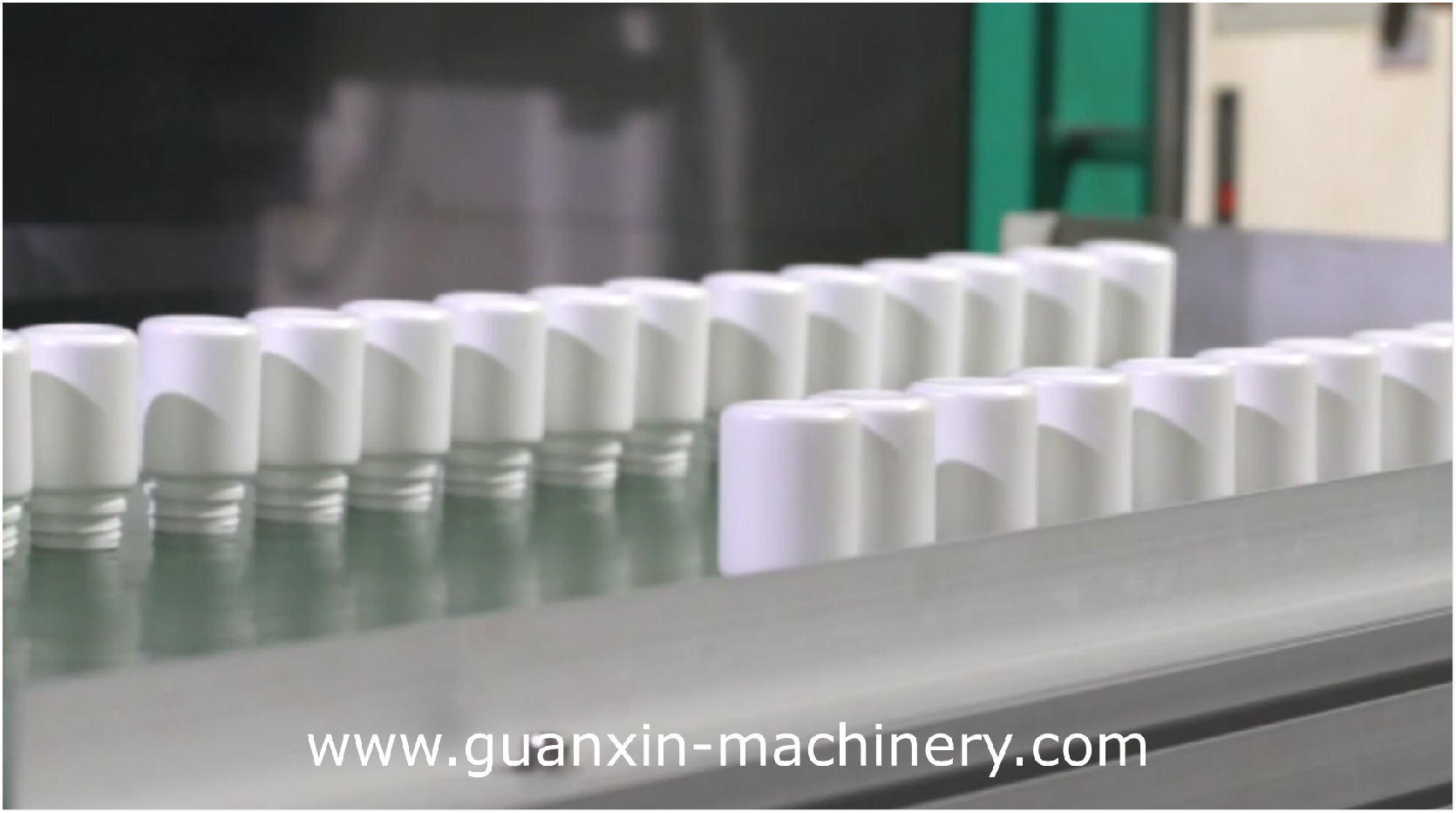
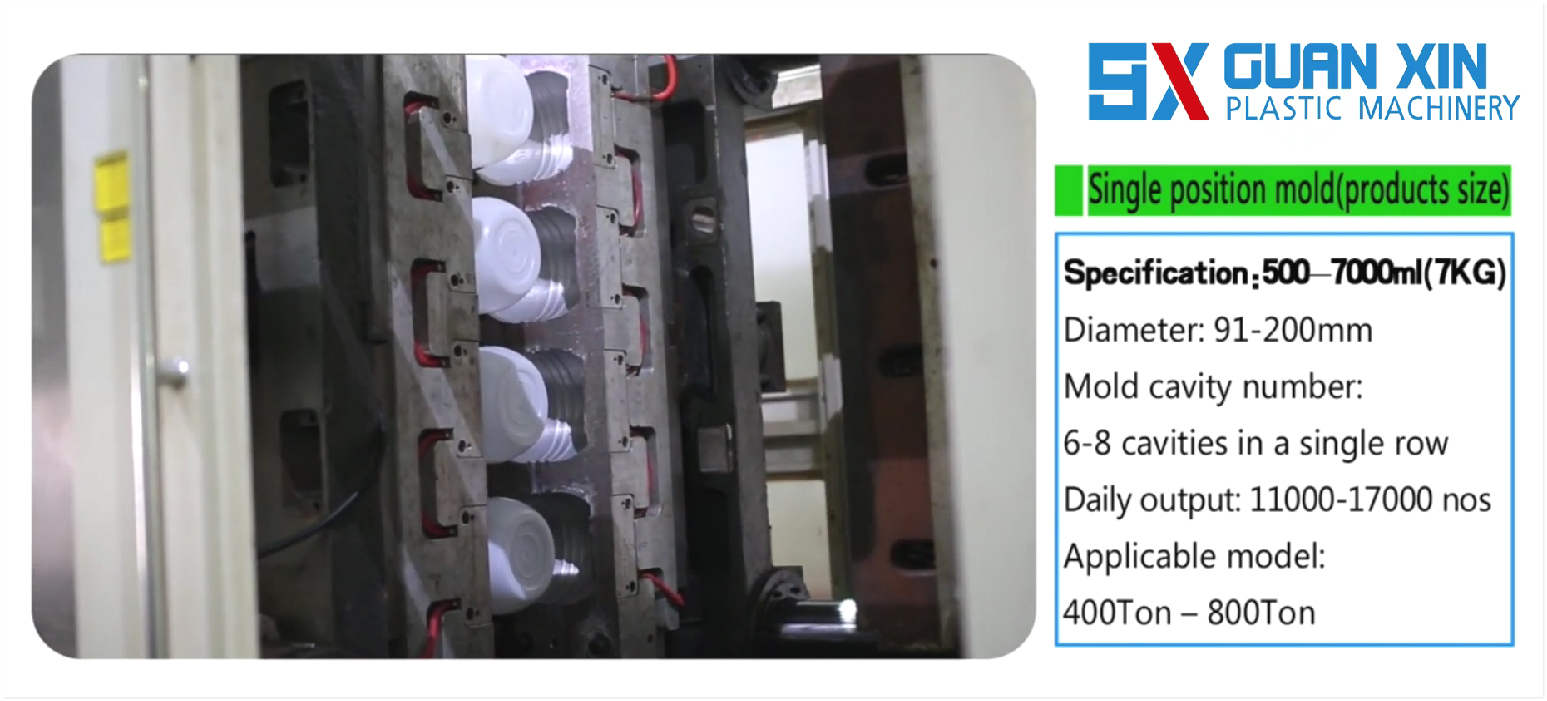
You need one injection molding machine only, with replacing different molds only to produce normal injection molding production, but also can make injection blow molding products like lots of bottles and plastic drums with different shapes in different materials PP, PE, PS, ABS, BAREX, PC, PVC, etc. Our injection blow molding system has very strong adaptability and a very high machine utilization rate, helping you expand the production line and bring down the manufacturing cost.
Why We Developed Horizontal Injection Blow Molding System
Our research found that there are 4 ways to produce bottles.
1. Produced by an extrusion blow molding machine
2. Two-step method: Made preform with an injection machine and then blow to bottle on a blow molding machine.
3. Vertical injection blow machines with the rotary platen and 3 WORKING STATIONS
4. Vertical injection blow machines with the rotary platen and 4 WORKING STATIONS
Both above solutions need additional blow molding machine or a new kind of extrusion blow molding machine for a traditional injection molding factory. But it causes big investment and high risk to expand their production line.
WE then picked this important piece and worked with engineers and developed new series of one step injection blow molding machines to fill the gap. To develop horizontal injection blowing molding machines with high output capacity, high quality but low manufacturing cost & very low investment & low risk. Helping our customer expand their market very quickly and gain great profits.
Now Guanxin Plastic Machinery offers a series of special plastic injection blowing molding machines with extremely competitive prices to help traditional injection molding manufacturers break into a new market.
What Is Horizontal Injection Blow Moulding System
A NEW PATENTED horizontal injection blowIing molding machine running with injection blow molding mold.
A NEW PATENTED mold combined with injection and blowing molding function into ONE mold.
High repeatability precision.
High speed and efficiency, energy-saving and stable, easy for operation and maintenance.
The hydraulic, pneumatic, and electrical controller is adjustable.
Suitable for most thermoplastic plastic, like PE, PP, PS, PC, etc.
The best solution for bottles used in the medical and food packing industry, and high appearance industry like LED lights diffuser, cosmetic bottles, etc.
How These One Step Injection Blowing Molding Machine Works
The preform is a precise shape, with precise wall thicknesses. After the one step injection molding machine open the clamp, then the blow mold cavity will be closed from two sides.
Compressed air is then injected into the center of the part, forcing the unsupported walls of the preform tube to stretch and expand outward, until they hit the walls of the blow mold. Once the material cools and solidifies, the mold is opened and the part is removed.
Injection blow molding allows for the production of hollow parts with some areas of the parts being very precise. Our one step injection blowing molding system can be running with high speed and output capacity. Like running 28 cavity injection blow mold with cycle time about 25 seconds. The output capacity is about 4000 pcs per hour.
Applications for injection blow molding include plastic bottles and plastic packaging with screw top lids.
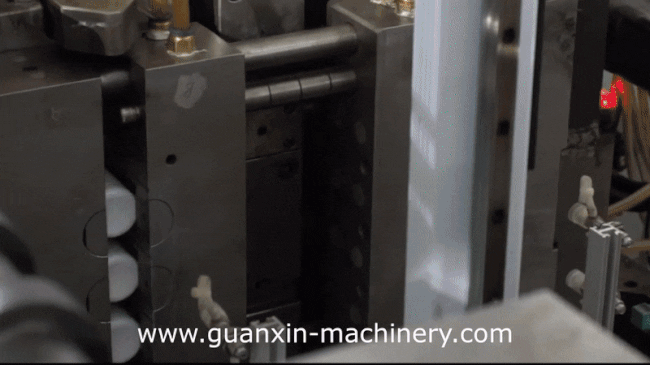
Applications of Horizontal Injection Blow Molding Products
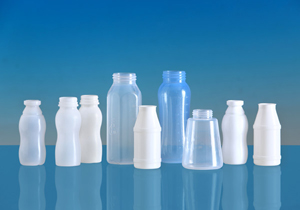
Baby Feeding Bottle
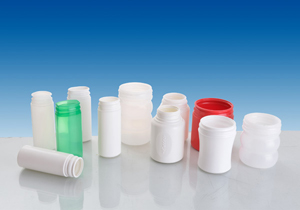
Chewing Gum Bottle
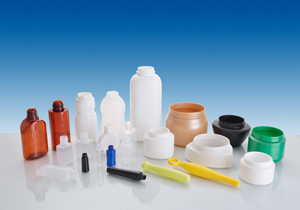
Comestic Bottles
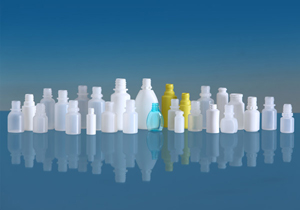
Eyedrops Bottles
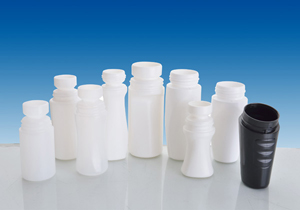
Roller Ball Bottle
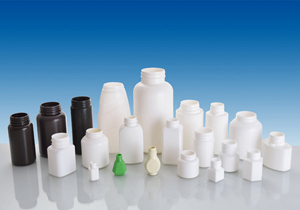
Tablet-Bottle
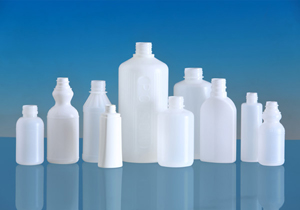
Pesticide Bottles
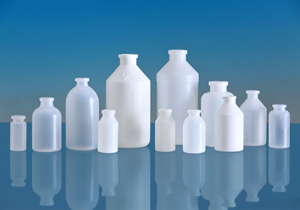
Medical Bottle
Injection Blow Molding VS Extrusion Blow Molding
Injection Blow Molding Technology
|
Extrusion Blow Molding Technology
|
No scrap |
20-40% scrap during production |
Uniform wall thickness |
Wall thickness variation |
Bottle weight variation of 1% |
Bottle weight variation of 3% |
Slower cycle time / more cavities |
Fast cycle time / less cavities |
Thin walls difficult to control |
Thick & thin wall capabilities |
Hollow Handleware not possible |
Hollow Handleware |
Necks made with injection molded tolerances |
Necks made with blow molded tolerances |
One technician per 4-6 machines |
One technician per 1-2 machines |
Process is controlled and repeatable with no adjustments |
Variable process requiring constant adjustment |
Almost no ancillary equipment |
Lots of ancillary equipment needed |
Advantages of Horizontal Injection Blow Molding System
3 Stations type
Injection Blow Molding
- 3 Sets Mold tooling works together.
- 3 Sets Mold have to be test one by one.
- Have to install 3 molds on 3 stations.
- Have to test 3 molds for production running.
- Difficult to switching to a start new project.
- Need a new vertical injection blow machine.
- More money investment for a new machine.
- Higher cost Products.
- One technician per 4-6 machines.
- Hardly to reach 28 cavity and above.
- Can run simple injection molding.
- Larger manufacturing space.
- NO Flash and energy saving.
ONE STEP
Injection Blow Molding Machine
- 1 Set Mold tooling only.
- 1 Set Mold have to be test only.
- Save time for replacing new molds.
- Save time for production running test.
- Very Easy to start a new project.
- Two in one IBM like normal IMM machine.
- Save money investment for machine.
- Competitive cost products.
- One technician per 6-10 machines.
- Easy to have 28 cavity and above.
- Can run as normal injection molding machine.
- Very small manufacturing space.
- NO Flash and energy saving.
Double Station
Extrusion Blow Molding Machine
- 2 Sets Mold tooling works together.
- 2 Sets Mold have to be test one by one.
- Have to install 2 molds on 2 stations.
- Have to test 2 molds for production running.
- Difficult to switching to a new project.
- Need a new extrution blow molding machine.
- More money investment for a new machine.
- Higher cost Products.
- One technician per 3-4 machines.
- Can`t reach 28 cavity and above.
- Do extrusion blow molding only.
- Largest manufacturing space.
- Have flash and waste a lot energy.